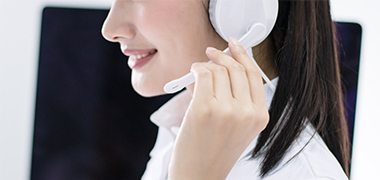
- 聯(lián)系人:許部長
- 聯(lián)系電話:13841408476
- 固定電話:024-44837288
- 公司傳真:024-44837004
- E-mail:xuming58@126.com
- 公司網(wǎng)址:wanderlustamericana.com
- 地 址:遼寧省本溪經(jīng)濟(jì)開發(fā)區(qū)香槐路110號
影響零件精度的誤差分析及控制措施
2023-05-16盧素琴
(陜西交通職業(yè)技術(shù)學(xué)院)
摘 要:零件的精度包括尺寸精度、表面粗糙度、幾何形狀和相互位置等。合理控制零件的加工精度,減小加工誤差是保證產(chǎn)品質(zhì)量的關(guān)鍵。本文系統(tǒng)分析了各種誤差及其產(chǎn)生原因,指出了提高零件加工精度的措施。
關(guān)鍵詞:零件精度;加工誤差;原因分析;控制措施
1.加工精度與加工誤差
1.1加工精度
是指零件加工后的實(shí)際幾何參數(shù)與理想幾何參數(shù)的符合程度。實(shí)際加工不可能做得與理想零件完全一致,總會有大小不同的偏差,零件加工后的實(shí)際幾何參數(shù)對理想幾何參數(shù)的偏離程度,稱為加工誤差。
1.2原始誤差
由機(jī)床、夾具、刀具和工件組成的機(jī)械加工工藝系統(tǒng)(簡稱工藝系統(tǒng))會有各種各樣的誤差產(chǎn)生,這些誤差在各種不同的具體工作條件下都會以各種不同的方式反映為工件的加工誤差。
工藝系統(tǒng)的原始誤差主要有工藝系統(tǒng)的幾何誤差、定位誤差、工藝系統(tǒng)的受力變形引起的加工誤差、工藝系統(tǒng)的受熱變形引起的加工誤差、工件內(nèi)應(yīng)力重新分布引起的變形以及原理誤差、調(diào)整誤差、測量誤差等。
1.3研究機(jī)械加工精度的方法
分析計(jì)算法和統(tǒng)計(jì)分析法。
2.工藝系統(tǒng)集合誤差
2.1機(jī)床的幾何誤差
加工中刀具相對于工件的成形運(yùn)動一般都是通過機(jī)床完成的,因此,工件的加工精度在很大程度上取決于機(jī)床的精度。機(jī)床制造誤差對工件加工精度影響較大的有:主軸回轉(zhuǎn)誤差、導(dǎo)軌誤差和傳動鏈誤差。機(jī)床的磨損將使機(jī)床工作精度下降。
2.1.1主軸回轉(zhuǎn)誤差
機(jī)床主軸是裝夾工件或刀具的基準(zhǔn),并將運(yùn)動和動力傳給工件或刀具,主軸回轉(zhuǎn)誤差將直接影響被加工工件的精度。
主軸回轉(zhuǎn)誤差是指主軸各瞬間的實(shí)際回轉(zhuǎn)軸線相對其平均回轉(zhuǎn)軸線的變動量。它可分解為徑向圓跳動、軸向竄動和角度擺動三種基本形式。
產(chǎn)生主軸徑向回轉(zhuǎn)誤差的主要原因有:主軸幾段軸頸的同軸度誤差、軸承本身的各種誤差、軸承之間的同軸度誤差、主軸繞度等。但它們對主軸徑向回轉(zhuǎn)精度的影響大小隨加工方式的不同而不同。
產(chǎn)生軸向竄動的主要原因是主軸軸肩端面和軸承承載端面對主軸回轉(zhuǎn)軸線有垂直度誤差。不同的加工方法,主軸回轉(zhuǎn)誤差所引起的的加工誤差也不同。在車床上加工外圓和內(nèi)孔時(shí),主軸徑向回轉(zhuǎn)誤差可以引起工件的圓度和圓柱度誤差,但對加工工件端面則無直接影響。主軸軸向回轉(zhuǎn)誤差對加工外圓和內(nèi)孔的影響不大,但對所加工端面的垂直度及平面度則有較大的影響。在車螺紋時(shí),主軸向回轉(zhuǎn)誤差可使被加工螺紋的導(dǎo)程產(chǎn)生周期性誤差。
適當(dāng)提高主軸及箱體的制造精度,選用高精度的軸承,提高主軸部件的裝配精度,對高速主軸部件進(jìn)行平衡,對滾動軸承進(jìn)行預(yù)緊等,均可提高機(jī)床主軸的回轉(zhuǎn)精度。
2.1.2導(dǎo)軌誤差
導(dǎo)軌是機(jī)床上確定各機(jī)床部件相對位置關(guān)系的基準(zhǔn),也是機(jī)床運(yùn)動的基準(zhǔn)。車床導(dǎo)軌的精度要求主要有以下三個(gè)方面:在水平面內(nèi)的直線度;在垂直面內(nèi)的直線度;前后導(dǎo)軌的平行度。
除了導(dǎo)軌本身的制造誤差外,導(dǎo)軌的不均勻磨損和安裝質(zhì)量,也使造成導(dǎo)軌誤差的重要因素。導(dǎo)軌磨損是機(jī)床精度下降的主要原因之一。
2.1.3傳動鏈誤差
傳動鏈誤差是指傳動鏈?zhǔn)寄﹥啥藗鲃釉g相對運(yùn)動的誤差。一般用傳動鏈末端元件的轉(zhuǎn)角誤差來衡量。
2.2刀具、夾具的制造誤差及磨損
任何刀具在切削過程中,都不可避免地要產(chǎn)生磨損,并由此引起工件尺寸和形狀的改變。正確地選用刀具材料和選用新型耐磨的刀具材料,合理地選用刀具幾何參數(shù)和切削用量,正確刃磨刀具,正確采用冷卻液等,均可有效地減少刀具的尺寸磨損。必要時(shí)還可采用補(bǔ)償裝置對刀具尺寸磨損進(jìn)行自動補(bǔ)償。
夾具的作用是使工件相對于刀具和機(jī)床具有正確的位置,因此夾具的制造誤差對工件的加工精度(特別是位置精度)有很大影響。夾具的制造誤差由定位誤差、夾緊誤差、夾具的安裝誤差、導(dǎo)引誤差、分度誤差以及夾具的磨損組成。夾具的磨損會引起工件的定位誤差。
2.3定位誤差
2.3.1 基準(zhǔn)不重合誤差
在零件圖上用來確定某一表面尺寸、位置所依據(jù)的基準(zhǔn)稱為設(shè)計(jì)基準(zhǔn)。在工序圖上用來確定本工序被加工表面加工后的尺寸、位置所依據(jù)的基準(zhǔn)稱為工序基準(zhǔn)。一般情況下,工序僚準(zhǔn)應(yīng)與設(shè)計(jì)基準(zhǔn)重合。在機(jī)床上對工件進(jìn)行加工時(shí),須選擇工件上若干幾何要素作為加工時(shí)的定位基準(zhǔn)(或測量基準(zhǔn)),如果所選用的定位基準(zhǔn)(或測量基準(zhǔn))與設(shè)計(jì)基準(zhǔn)不重合,就會產(chǎn)生基準(zhǔn)不重合誤差?;鶞?zhǔn)不重合誤差等于定位基準(zhǔn)相對于設(shè)計(jì)基準(zhǔn)在工序尺寸方向上的Z大變動量。
2.3.2定位副制造不準(zhǔn)確誤差
工件在夾具中的正確位置是由夾具上的定位元件來確定的。夾具上的定位元件不可能按基本尺寸制造得準(zhǔn)確,它們的實(shí)際尺寸(或位置)都允許在分別規(guī)定的公差范圍內(nèi)變動。同時(shí),工件上的定位基準(zhǔn)面也會有制造誤差。工件定位面與夾具定位元件共同構(gòu)成定位副,由于定位副制造得不準(zhǔn)確和定位副間的配合間隙引起的工件Z大位置變動量,稱為定位副制造不準(zhǔn)確誤差。
2.4工藝系統(tǒng)受力變形引起的誤差
工藝系統(tǒng)是一彈性系統(tǒng),在加工時(shí)由于切削力、夾緊力和傳動力等作用會產(chǎn)生相應(yīng)變形破壞了刀具和工件間的正確位置,從而產(chǎn)生加工誤差。
2.4.1切削過程中受力點(diǎn)位置變化引起的加工誤差
切削過程中,工藝系統(tǒng)的剛度隨切削力著力點(diǎn)位置的變化而變化,引起系統(tǒng)變形的差異,使被加工表面產(chǎn)生形狀誤差。
2.4.2切削力大小變化引起的加工誤差——誤差復(fù)映
工件的毛坯外形雖然具有粗略的零件形狀,但它在尺寸、形狀以及表面層材料硬度上都有較大的誤差。毛坯的這些誤差在加工時(shí)使切削深度不斷發(fā)生變化,從而導(dǎo)致切削力的變化,進(jìn)而引起工藝系統(tǒng)產(chǎn)生相應(yīng)的變形,使得零件在加工后還保留與毛坯表面類似的形狀或尺寸誤差。當(dāng)然工件表面殘留的誤差比毛坯表面誤差要小得多。這種現(xiàn)象稱為“誤差復(fù)映規(guī)律”,所引起的加工誤差稱為“誤差復(fù)映”。除切削力外,傳動力、慣性重力、夾緊力等其它作用力也會使工藝系統(tǒng)的變形發(fā)生變化,從而引起加工誤差,影響加工精度。
2.5工藝系統(tǒng)受熱變形引起的誤差
機(jī)械加工中,工藝系統(tǒng)在各種熱源的作用下產(chǎn)生一定的熱變形。由于工藝系統(tǒng)熱源分布的不均勻性及各環(huán)節(jié)結(jié)構(gòu)、材料的不同,使工藝系統(tǒng)各部分的變形產(chǎn)生差異,從而破壞了刀具與工件的準(zhǔn)確位置及運(yùn)動關(guān)系,產(chǎn)生加工誤差。尤其對于精密加工,熱變形引起的加工誤差占總加工誤差的40%~70%。
2.5.1機(jī)床熱變形對加工精度的影響
機(jī)床受熱源的影響,各部分溫度將發(fā)生變化,由于熱源分布的不均勻和機(jī)床機(jī)構(gòu)的復(fù)雜性,機(jī)床的各部件發(fā)生不同程度的熱變形,破壞了機(jī)床各部件原有的相互位置關(guān)系,影響加工精度。不同類型的機(jī)床由于熱源不同,對加工精度影響也不同。
2.5.2刀具熱變形對加工精度的影響
盡管在切削加工中傳入刀具的熱量只有3%~5%,但由于刀具的尺寸和熱容量小,故仍有很高的溫升,從而引起刀具的熱伸長并造成加工誤差。粗加工時(shí)刀具的熱變形對加工精度的影響可忽略不計(jì);對于加工要求較高的零件,刀具的熱變形對加工精度影響較大,使加工表面產(chǎn)生形狀誤差。例如用高速鋼刀具車削時(shí),刃部的溫度高達(dá)700℃~800℃,刀具熱伸長量可達(dá)0.03mm。
2.6調(diào)整誤差
在機(jī)械加工的每一工序中,總要對工藝系統(tǒng)進(jìn)行這樣或那樣的調(diào)整工作。由于調(diào)整不可能的準(zhǔn)確,因而產(chǎn)生調(diào)整誤差。在工藝系統(tǒng)中,工件、刀具在機(jī)床上的互相位置精度,是通過調(diào)整機(jī)床、刀具、夾具或工件等來保證的。當(dāng)機(jī)床、刀具、夾具和工件毛坯等的原始精度都達(dá)到工藝要求而又不考慮動態(tài)因素時(shí),調(diào)整誤差的影響,對加工精度起到?jīng)Q定性的作用。
2.7測量誤差
零件在加工時(shí)或加工后進(jìn)行測量時(shí),由于測量方法、量具精度以及工件和主客觀因素都直接影響測量精度。
2.8加工原理誤差
加工過程由于采用了近似的加工方法,近似的傳動或近似的刀具輪廓而產(chǎn)生的加工誤差。
2.8.1采用近似的加工運(yùn)動造成的誤差
在許多場合,為了得到要求的工件表面,必須在工件或刀具的運(yùn)動之間建立一定的聯(lián)系。從理論上講,應(yīng)采用完全準(zhǔn)確的運(yùn)動聯(lián)系。但是采用理論上完全準(zhǔn)確的加工原理有時(shí)使機(jī)床或夾具極為復(fù)雜,致使制造困難,反而難以達(dá)到較高的加工精度,有時(shí)甚至是不可能做到。如在車削或磨削模數(shù)螺紋時(shí),由于其導(dǎo)程t=πm,式中有π這個(gè)無理因子,在用配換齒輪來得到導(dǎo)程數(shù)值時(shí),就存在原理誤差。
2.8.2采用近似的刀具輪廓造成的誤差
用成形刀具加工復(fù)雜的曲面時(shí),要使刀具刃口做得完全符合理論曲線的輪廓,有時(shí)非常困難,往往采用圓弧、直線等簡單近似的線型代替理論曲線。如用滾刀滾切漸開線齒輪時(shí),為了滾刀的制造方便,多用阿基米德基本蝸桿或法向直廓基本蝸桿來代替漸開線基本蝸桿,從而產(chǎn)生了加工原理誤差。
3.提高零件加工精度的措施
3.1減少原始誤差
提高零件加工所使用機(jī)床的幾何精度,提高夾具、量具及刀具本身精度,控制工藝系統(tǒng)受力、受熱變形、刀具磨損、內(nèi)應(yīng)力引起的變形、測量誤差等均屬于直接減少原始誤差。為了提高機(jī)械加工精度,需對產(chǎn)生加工誤差的各項(xiàng)原始誤差進(jìn)行分析,根據(jù)不同情況對造成加工誤差的主要原始誤差采取不同的措施解決。對于精密零件的加工應(yīng)盡可能提高所使用精密機(jī)床的幾何精度、剛度和控制加工熱變形;對具有成形表面的零件加工,則主要是如何減少成形刀具形狀誤差和刀具的安裝誤差。
3.2誤差補(bǔ)償法
對工藝系統(tǒng)的一些原始誤差 ,可采取誤差補(bǔ)償?shù)姆椒ㄒ钥刂破鋵α慵庸ふ`差的影響。
(1)誤差補(bǔ)償法:此法是人為地造?一種新的原始誤差,從而補(bǔ)償或抵消原來工藝系統(tǒng)中固有的原始誤差,達(dá)到減少加工誤差,提高加工精度的目的。
(2)誤差抵消法:利用原有的一種原始誤差去部分或全部地抵消原有原始誤差或另一種原始誤差。
3.3分化或均化原始誤差
為了提高一批零件的加工精度,可采取分化某些原始誤差的方法。對加工精度要求高的零件表面,還可以采取在不斷試切加工過程中,逐步均化原始誤差的方法。
(1)分化原始誤差(分組)法:根據(jù)誤差反映規(guī)律,將毛坯或上道工序的工件尺寸經(jīng)測量按大小分為n組,每組工件的尺寸范圍就縮減為原來的1/n。然后按各組的誤差范圍分別調(diào)整刀具相對工件的準(zhǔn)確位置,使各組工件的尺寸分散范圍中心基本一致,以使整批工件的尺寸分散范圍大大縮小。
(2)均化原始誤差:此法過程為通過加工使被加工表面原有誤差不斷縮小和平均化的過程。均化的原理就是通過有密切聯(lián)系的工件或工具表面的相互比較和檢查,從中找出它們之間的差異,然后再進(jìn)行相互修正加工或基準(zhǔn)加工。
3.4轉(zhuǎn)移原始誤差
這種方法的實(shí)質(zhì)就是將原始誤差從誤差敏感方向轉(zhuǎn)移到誤差非敏感方向上去。轉(zhuǎn)移原始誤差至非敏感方向。各種原始誤差反映到零件加工誤差上的程度與其是否在誤差敏感方向上有直接關(guān)系。若在加工過程中設(shè)法使其轉(zhuǎn)移到加工誤差的非敏感方向,則可大大提高加工精度。轉(zhuǎn)移原始誤差至其他對加工精度無影響的方面。
4.結(jié)束語
在機(jī)械加工中,誤差是不可避免的,只有對誤差產(chǎn)生的原因進(jìn)行詳細(xì)的分析,才能采取相應(yīng)的預(yù)防措施減少加工誤差,提高零件加工精度。
參考文獻(xiàn):
[1] 熊良山,嚴(yán)曉光,張福潤.機(jī)械制造技術(shù)基礎(chǔ)[M].華中科技大學(xué)出版社,2009,4.
[2] 汪堯,工藝系統(tǒng)幾何誤差對加工精度的影響分析[J].科技信息,2004(4).
(來源:科園月刊)
(版權(quán)歸原作者或機(jī)構(gòu)所有)