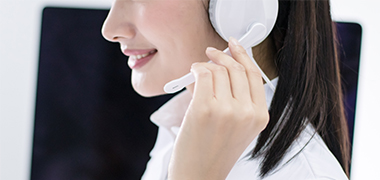
- Contact:Minister Xu
- Mobile:13841408476
- Tel:024-44837288
- Fax:024-44837004
- E-mail:xuming58@126.com
- Web:wanderlustamericana.com
- Address:No.110 XiangHuai Road
Benxi Economic Development Zone
Liaoning Province
Desktop Engineering – How to Calculate Dynamic and Static Load Ratings
29 Nov,2019
Introduction When comparing bearing suppliers, engineers are often left with few options other than to compare dynamic load ratings and corresponding life calculations. Of course, we can look at steel and manufacturing quality; but if we are comparing sources of similar quality, those items may not provide a large contrast. It often surprises people to learn that bearing capacities are calculated values, not tested values. Lately, however, a trend is emerging for bearing suppliers to increase their ratings for higher performance bearings that have premium features such as higher quality steel and specilaized heat treatment. Bearing companies are under intense competitive pressure to make every feature add to the dynamic capacity of their bearings because it is very well understood that an increase in capacity adds to the bottom line. As a result, it is important that the end user develop a keen understanding of how capacity ratings and subsequent life calculations are generated in order to make a true comparison, or be left to comparing the claims of well-heeled marketing departments.
Dynamic Capacity
Nearly every calculation surrounding bearing life begins with the dynamic capacity, Cr. Cr is the equivalent load that would result in an average service life of one million revolutions. The formula is imperfect and standard bearings aren’t designed to handle 100% of Cr; but, those are annoying nuances we have to understand and live with. In the past, most bearing companies would follow the dynamic capacity formula to ISO or ABMA standards and then increase the resulting life calculation by some factor based on heat treatment and other premium features in addition to the increase that would come through ISO 281 or 16281 using a-iso factors. The issues that end users have with this is that enhanced life calculation factors are not always shown on the bearing print and the print is the primary legal document that exists between the end user and the bearing manufacturer. Some end users interpret this as being an escape route for the bearing companies if something goes wrong – which it is not. Consequently, the competition and end users are pushing bearing companies to increase capacity ratings on the print. This is where the math starts getting fuzzy. We will walk through the formula with a couple of real bearings and determine where these numbers are coming from.
For this example, let’s look at two high-quality competitors, each producing their own design of the HM804846/10, a popular inch-series tapered roller bearing. We’ll refer to these as Company A and Company B.
Right off, we see bm is defined by ISO as 1.1. For i, both bearings have 1 row; i = 1. The bearing half-angle, a, will be provided by the manufacturer, so we can skip that measurement. Both of these bearings are around 20° (though a side-by-side comparison clearly shows they are not identical angles). Z, the number of rollers, is easy enough to count — both have 18 rollers. The remaining values — fc, Lwe, Dwe and Dpw — are often not provided, but we can physically measure these features. Customer models will typically leave off just enough features to prevent an accurate measurement. We could get fancy and have these set up on a CMM and measure to 3 decimal places, but if you glance at the load ratings in the catalog you will see everything is rounded to the nearest 500 N. None of these factors will change your results greater than the rounding error if you are within 0.5 mm of accuracy. This sounds like a job for calipers.
We will skip fc for now because that is a tabulated value which we need two of our other unknowns for. Let’s start with the effective roller length Lwe. ABMA defines Lwe as:
The theoretical maximum length of contact between a roller and that raceway where the contact is shortest. NOTE: This is normally taken to be either the distance between the theoretically sharp corners of the roller minus the roller chamfers, or the raceway width excluding the grinding undercuts — whichever is the smaller.