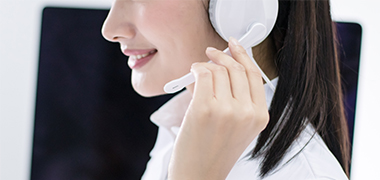
- Contact:Minister Xu
- Mobile:13841408476
- Tel:024-44837288
- Fax:024-44837004
- E-mail:xuming58@126.com
- Web:wanderlustamericana.com
- Address:No.110 XiangHuai Road
Benxi Economic Development Zone
Liaoning Province
High-quality sensor data for Industry 4.0
17 Oct,2019
Knowing what types of sensors to use and what data to collect can drive connectivity and process efficiency.
Sensor technology is the prerequisite for implementing Industry 4.0. Sensors collect data on process and machine statuses, making it available for process-relevant information services and workflows. However, sensor costs and the variety of possible applications often make it difficult for users to appreciate the economic benefit.
The Mechanical Engineering Industry Association (VDMA), in cooperation with the Wbk Institute of Production Science of the Karlsruhe Institute of Technology (KIT) compiled the Sensors for Industry 4.0 guideline to highlight various tools and methods for lowering sensor costs.
“Sensors are the links between the digital and the real world and therefore one of the most important factors in the implementation of Industry 4.0. All higher-level data interpretation systems are blind without the right sensors,” says professor Jürgen Fleischer, one of the guide’s main contributors.
Ball screw lubrication
Fleischer says KIT projects show how information can be usefully captured and processed using sensors.
“Data can be captured in the drive components of machine tools to monitor their condition and optimize operation,” Fleischer says. “In ball screws, for example, the axial force and the friction torque on the ball screw nut can be measured. The exact lubrication requirement can then be determined by comparing the results with a model for friction behavior.”
He adds that KIT researchers developed an adaptive lubrication system that uses sensor data to significantly increase the service life of ball screws in tests. And in addition to lubrication controls, different drive components can be monitored by capturing structure-borne noise.
“These signals change throughout a component’s lifetime and allow conclusions to be drawn on the state of wear. The goal is predictive, condition-based maintenance, also known as predictive maintenance,” Fleischer says.
Software analysis
However, implementing algorithms to analyze sensor data and determine relevant features for automatic evaluation can be time intensive. Xeidana software, developed at the Fraunhofer Institute for Machine Tools and Forming Technology (IWU) in Chemnitz, performs data acquisition and automated quality control.
The software detects surface defects accurately in real-time using optical sensors (such as multi-camera systems). The data can then be fed back to the production system to enable a quick response if process parameters are breached.
Further examples of real-time capture of sensor data at the IWU include pressing, punching, and cutting forces recorded in forming machine tools.
Real-time sensor data
Whether or not to capture sensor data in real-time depends on the application.
“You have to identify the point up to which real-time capture makes sense, how the data is synchronized, and which sampling rates are necessary to obtain an accurate process description,” says Dr. J?rg Stahlmann, managing director of Consenses, an industrial measurement technology and digitalization solutions company. “We use 3D step models to understand our customers’ designs and to classify sensor data – such as the expected force and temperature flows – and kinematics correctly.”
Simulations can also be beneficial to making sense of sensor data.
“Simulations of components, assemblies, and machines give us a better understanding of the mechanical effects encountered in production plants,” Fleischer says. “We use this knowledge to make targeted use of sensors and to interpret the captured data more efficiently.”
However, not every application requires real-time capture, and there are certain instances where real-time data is not the most efficient.
“Real-time data is often provided by control units which originally collected it to control certain machine actions,” Stahlmann says. This goal does not always overlap with the requirements for the sensor data. Before far-reaching analyses or decisions are derived from this data, it is important to understand which signal is generated in each individual case. For example, in condition-based maintenance, real-time recording is superfluous.
“Condition-based maintenance does not require a rapid response to the collected data. The results of the data evaluation may even be delivered several hours after the data has been entered. Recorded data can be stored in a buffer so that it can be aggregated and evaluated at a later point in time, and the evaluation can be outsourced to a powerful server,” Fleischer says.
“If there is no economic justification, there is no need for real time,” says Dr. Thomas P??ler, forming machines group manager at IWU. “Real-time capture is not necessary for trend analyses conducted over a longer period. It is not necessary to keep all the data; only individual parameters should be generated and archived. In addition, there is little to be gained from capturing data required for management purposes in real-time, including parameters related to the economic efficiency of production, such as how many components of a particular type were produced on one plant.”
The German Academic Association for Production Technology (WGP) also addressed the question of meaningful and appropriate automation in its Industriearbeitsplatz 2025 paper, concluding that “all technical possibilities should be exploited in the economic value creation process, but maximum automation is not always necessary or useful.”
However, real-time sensor data is inevitably necessary for machine, tool, or workpiece protection or process stability.
“Real-time data capture is indispensable when it’s the only way to prevent damage,” P??ler says. “This applies in the case of tool breakage or excessive stress on assemblies such as bearings or frame components. In order to preclude the possibility of any rejects, it makes sense to capture the material properties in real-time with the appropriate sensors.”
Real-time detection can also help prevent damage to workpieces during production and rectify any errors made during setup.
“Errors made during the setup of machine tools or in the NC program can lead to collisions,” Fleischer says. “If these are detected quickly enough, the machine can be stopped, and material damage reduced.”
Linked sensor data
Scientists at the IWU use real-time monitoring of forces, paths, and stretching on forming presses. Rather than being evaluated individually, these different types of data are fed into Smart Stamp, a software-based analysis module, where they are merged and analysed. By combining data, manufacturers can know if the press is working in its normal range, if the tool is wearing too quickly, or if the ram mounted on the upper tool has a critical tilt that could mar the workpiece.
However, there are points on the machine where it is not possible to mount real sensors, as they would be difficult to access, or installation would be too complicated and expensive. There may be no relevant data available for particular processes and machine statuses. The IWU solution is to use virtual sensors.
Real sensors, mounted at different points on the machine, serve as the basis of this technology, and a digital twin in the form of a virtual sensor is created from their measured values. This calculates the values that a real sensor would record at a relevant but inaccessible location.