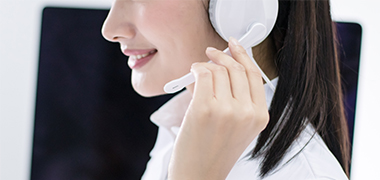
- Contact:Minister Xu
- Mobile:13841408476
- Tel:024-44837288
- Fax:024-44837004
- E-mail:xuming58@126.com
- Web:wanderlustamericana.com
- Address:No.110 XiangHuai Road
Benxi Economic Development Zone
Liaoning Province
What’s Up Doug? A seal that prevents ingress into bearings in harsh environments
23 Sep,2019
Most people involved in belt conveyors, especially those used in mining and oil sands or heavy equipment operations have heard of “taconite” seals in the bearing pillow blocks (housings) of the pulleys.
Taconite is a form of iron ore. It is a sedimentary form of iron ore made up mostly of magnetite, hematite and chert. Magnetite and hematite are very abrasive and have been used as an abrasive in the manufacturing industry. The pulleys of the belt conveyors used to transport the ore in a taconite mine suffer terribly due to taconite dust.
To overcome the problem of the highly invasive taconite material penetrating bearing housings, engineers came up with a taconite seal that prevents ingress into the bearings in harsh environments. Taconite seals take their name from iron ore mined in Minnesota’s Mesabi Range in the United States.
Taconite seals are not standardized components. While they are often perceived to be standard part, they are not. This misperception creates confusion and a lack of continuity as a design engineer may specify a taconite seal intending to get one design, but what is sourced (often from the lowest bidder) is not what the designer intended.
The only common thread a taconite seal shares with other comparable seals is that it is a grease-purgeable seal, meaning grease is injected directly into the seal and then flows out by pushing the contamination away from the bearing. This is a key distinction in that the housing has two or three grease inlets – one per seal and one for the bearing. It is not enough to hope that the grease going into the bearing is also enough to purge the seals. Each seal must have grease added to it.
Designed for purpose
There are two major general designs: a one-piece taconite seal and a two-piece taconite seal. The one-piece design is a single piece of steel that attaches to the housing and is stationary. Within the stationary ring could be a piece of felt or a lip seal of some sort. The disadvantage with this shaft contact seal is the probability of grooving of the shaft, which can be more pronounced when there is abrasive contamination. The one-piece taconite seal tends to be the “economy” solution since it is only one part and this is a prime example of where the specification of taconite seal may cause disappointment with the performance of a taconite seal.
The second general type of taconite seal is a two-piece taconite seal and consists of a stator (adapter ring) and a rotor (flinger ring), which mate together with some form of axial or radial labyrinth and possibly a lip seal. In this case, the lip runs on the seal component instead of the shaft as not to wear the shaft.
There are two generations of two-piece taconite seals. With the first generation, there was an attempt to save space and have a narrow width across the seals. To accomplish this, the stator fit into a housing with an enlarged seal opening. However, once this seal opening was changed to accommodate the taconite seal, it could not be used with a standard triple labyrinth seal.
From this arose the generation-two taconite seals. In this version, the stator fits into the standard seal groove, which accommodates the triple labyrinth seal fit. The overall width became wider, however the second-generation taconites can fit into off-the-shelf housings.
So, is the generation two taconite the “be all end all”? The answer is no. In Australia, a large mining operation has tested it and found that the next level of reliability improvement came with the combination of using sealed spherical roller bearings along with the taconite seals. The bearing seals retain the high quality, clean grease in the bearing, the grease in the housing provides a second barrier and the taconite seal provides the best third barrier from external contamination.
A few things to keep in mind
There is no standard for a taconite seal other than it being a grease-purgeable seal (and this is not governed my any technical association). The individual design of the seal can offer important features that can make a difference in the performance, such as avoidance of shaft wear and more effective sealing due to complexity of labyrinths. No matter what design, a taconite seal that does not get fed grease is essentially ineffective. And, the most effective known sealing solution in a mining and oil sands operations is a combination of a sealed spherical roller bearing and a taconite (concept) seal.