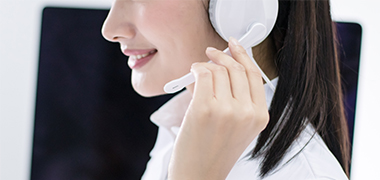
- Contact:Minister Xu
- Mobile:13841408476
- Tel:024-44837288
- Fax:024-44837004
- E-mail:xuming58@126.com
- Web:wanderlustamericana.com
- Address:No.110 XiangHuai Road
Benxi Economic Development Zone
Liaoning Province
The fall of friction in bearings?
12 Sep,2019
Design engineers have long searched for material coating methods to reduce friction. But, could the restructuring of newly found materials reduce friction on macroscopic scales? Here, Chris Johnson, managing director of EZO bearings supplier SMB Bearings, explains how future surface treatments, including innovations in graphene and graphene-related materials (GRM) could enable better, or limitless, bearing wear.
Frequently encountered in many industries and sectors, friction is a fact of life. Rolling, rotating or sliding contact interfaces in every human-made, natural, or biological system will generate friction. If not reduced or controlled effectively, excess friction often leads to higher wear losses and ultimately, poor reliability and lifespan.
Friction’s most basic definition is the force that prevents smooth and easy movement of two moving surfaces in contact with each other. With friction comes wear and tear, and thus, lubricants in a liquid or solid form are needed to prevent this. However, friction can be a complex problem for engineers — bearing friction is not constant and is addressed using certain tribological phenomena that occur in the lubricant film between the rolling elements, raceways, and cages.
A proper lubricant will reduce friction between the internal sliding surfaces of the bearing’s components and reduce or prevent metal-to-metal contact of the rolling elements within their raceways. While this is a good way of reducing wear and preventing corrosion, there are new materials that, when used on bearings, dramatically reduce friction compared to the lubrication and surface treatment options that are currently on the market.
Superlubricity
On the macroscale, friction is the result of microscopic imperfections in surfaces. On the atomic-scale, however, friction concerns the attractive forces between individual atoms. This relationship opens up the phenomenon of superlubricity; where the atomic-scale structural mismatch makes it impossible for multiple atoms in one surface to get close to atoms in the other, leading to extraordinarily low friction.
Since superlubricity was first proposed in 1990, several groups have observed the effect, but it has been difficult to scale because of the inconsistency between macroscopic surfaces. That is, until now.
Graphite was used in early investigations due to its layered lattice-like properties. Imagine egg cartons; when the cartons are aligned, they stick together inside one another, but if they’re out of alignment, they do not stick, and they can easily slide over one another. Graphite’s lattice composition, somewhat comparable to these stacks of egg cartons, makes a great candidate to further these investigations into superlubricity.
Graphene and GRM
Graphene and its tribological potential as a lubricant remains relatively unexplored, with few investigations into its use as a self-lubricated solid or as an additive for lubricating oils. With graphene being a two-dimensional material, it offers unique friction and wear properties that are typically not seen conventionally. Besides its well-established thermal, electrical, optical, and mechanical properties, graphene can serve as a liquid or colloidal lubricant for bearings and can even be applied as flakes to the surface.
Because graphene is ultrathin even with multiple layers, it can be applied to systems with oscillating, rotating and sliding contacts to reduce friction and wear, as well as protecting bearings from corrosion when exposed to water, a process commonly known as tribo-corrosion. This is due to graphene exhibiting a slippery texture, which could potentially make it an excellent lubricant.
As well as being low shear and highly protective, the application of graphene in bearings prevents oxidation of the steel surfaces due to its relative lack of permeability to liquids and gases. Research shows that the small number of layers in graphene not only reduces friction in steel seven times more but also wear-and-tear 10,000 times more, reducing tribo-corrosion.
The process of adding a graphene coating to bearings is relatively simple compared to adding a traditional lubricant — graphene does not require any additional processing steps, other than just sprinkling a small amount of solution or spraying the solution on the surface, making this process simple, environmentally friendly and cost-effective.
As well as not being harmful to the environment, graphene flakes that are added to the surface of a bearing can last a considerable amount of time, due to the ability of the flakes to reorient themselves during the initial wear cycles, providing a very low coefficient of friction (COF).
In a study on the potential of graphene as a new emerging lubricant, researchers estimated that the reduced loss of energy to friction offered by new materials would yield potential energy savings of 2.46 billion kilowatt-hours per year, equivalent to 1.5 million barrels of oil.
It is evident that innovations in graphene and newly discovered materials have potential as both solid and liquid lubricants for bearings. Once fully developed, these new lubrication options could have positive impacts on many applications that could lead to tremendous energy savings.