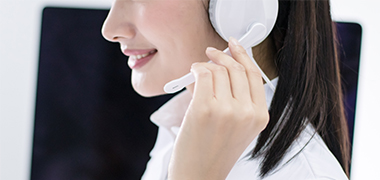
- Contact:Minister Xu
- Mobile:13841408476
- Tel:024-44837288
- Fax:024-44837004
- E-mail:xuming58@126.com
- Web:wanderlustamericana.com
- Address:No.110 XiangHuai Road
Benxi Economic Development Zone
Liaoning Province
How Harmonic Bionics designs lightweight, upper-body exoskeletons
05 Sep,2019
In human anatomy, the shoulder presents one of the most challenging and complex physical problems for physicians and therapists. Shoulders and their intricate anatomical patterns also provide a unique test for developers of exoskeletons, who need to keep their units light and compact while incorporating an extensive range of movement.
Those were the challenges faced by Austin, Texas-based Harmonic Bionics. Building upon the fundamental research carried out in the Mechanical Engineering Department at The University of Texas, Harmonic Bionics designed an exoskeleton, called Harmony, that tracks the shoulder joint as well as the scapular movement of the shoulder girdle. The exoskeleton maximizes the range of motion of the human shoulder and the shoulder girdle while ensuring safety with physical and programmed interlocks. Actuator and controller technology allow Harmony to customize gravity compensation, assistance and impedance as needed for the patient.
Harmony is a treatment and therapy device that allows therapists to work with the patients to improve the functionality and healing from neuromuscular damage. It is especially helpful for victims of stroke. There are more than 800,000 new cases of stroke every year in the United States alone.
“Development of robust closed-loop torque-controlled actuators with high refresh rates was our biggest challenge,” said Rohit John Varghese, Harmonic Bionics’ Head of Product Development. “The design team built out all of the motor control and communication electronics in-house, and this has enabled the level of performance that the therapist who we work with require.”
“Our robotic solution frees the therapist to do what they do best and that is to interact with the human, which is an underrated but critical part of the recovery process,” Varghese added. “It creates an intimate dynamic between the therapist, the patient and the robot. The result is that survivors of stroke will get better faster and more effectively.”
Examining Harmonic Bionics’ exoskeleton
The project began in the ReNeu Robotics Lab at The University of Texas’ Cockrell School of Engineering in 2011 with funding from National Science Foundation and NASA. “The critical piece in Harmony is a novel shoulder mechanism that powers coordinated motions of five joints in the shoulder complex, which is the key to shoulder rehabilitation,” said Ashish Deshpande, director of the ReNeu Robotics Lab. Ensuring alignment between the exoskeleton and the patient is critical to prevent stress on the patient’s joints and protect them from injury.
Each side of the robot seamlessly moves the subject’s arm and shoulder through full natural range of motion, and it can be adjusted for people of all shapes and sizes. Harmonic Bionics used information from NASA databases to collect its anthropometric size data, based on which Harmony has been designed to adjust its size to fit more than 95 percent of the American population.
To be effective in a clinical setting, it is important for the exoskeleton to quickly and smoothly change its physical dimensions to align with these different body sizes. Oil-based lubrication for the linear bearings cause many issues, including the accumulation of dirt, which allows for bacteria to accumulate.
High-performance plastics
In addition, due to the complexity of the robot, the resizing mechanisms need to be highly compact to allow room for the electronics and actuators. All linear bearing mechanisms need to be able to lock once in position to prevent unwanted changes in size.
Harmonic Bionics solved multiple issues by choosing linear bearings from igus, a Germany-based manufacturer of motion plastics. The company runs its North American operations out of Providence, R.I. The company’s products are lubrication- and maintenance-free. The bearings allow for smooth and bind-free size adjustment without lubrication, and size and weight reduction.
Harmony includes 6 of igus’ iglide J bearings, a versatile endurance performer that exhibits low wear against different shaft materials and low coefficients of friction in dry operation. They are cost-effective bearings when low-pressure loads are needed, and are frequently used in automation, printing, beverage technology and aerospace engineering.
A custom bearing housing compresses on a dryLin R liner, which reduced the size significantly compared to previous models of the exoskeleton. Compression from the housing locks shafts, eliminating the need for an additional shaft collar. dryLin R products are made with the iglide J materials, and are frequently used in packaging, 3D printing, and laboratories. The shoulder mechanism also includes DryLin R bearings, which operate dry and tolerate frequent cleanings.
DryLin-T rail guide systems manufactured by igus ensure high rigidity in the stand for the exoskeleton. The guides are extremely resistant to dirt and offer a low coefficient of friction and wear. They are also frequently used in machine building, machine tools, package handling and the woodworking industry.
Tackling the shoulder
Several factors played into Harmonic’s decision to focus on the development of the exoskeleton for shoulders. First, the staggering incidences of strokes figures to rise over the next 10 years and has been increasing significantly.
“As medical care gets better, people live longer,” Deshpande said. “Also, trend lines show incidences of stroke among younger populations. The result is lost productivity and longer durations of suffering.”
Many therapy and assistive devices have focused on ambulation – improved functionality of the legs. “Thanks to the success of the ADA in the United States, a lot of that problem is being solved with wheelchair accessibility,” Deshpande said. But the next stage to enabling the basic activities of daily living, is helping stroke survivors and other people with neuromuscular diseases to become more independent and restore function to the upper body.
Finally, research on improving physical therapy techniques of the shoulders if greatly hindered by the highly subjective metrics that are used for assessment of recovery.
“The gold standard assessment scale for recovery is still a subjective assessment by the therapist on the scale of 1-5,” Varghese said. “It’s difficult to come up with an alternative form of measurement without a device like Harmony, especially for the shoulder. It’s such a complicated join. Not just the ball and socket, but the complex motion of the shoulder girdle as well. We must make sure the arm and the shoulder move in coordination. The exoskeleton re-teaches that coordination.”
Solving the challenges
The entire scope of the project posed significant challenges for the team at Harmonic. The complexities of the shoulder movements, safety of patients and finding durable, lubrication-free components made the design of the device a time consuming and laborious process.
But with stroke such a serious and widespread medical concern, the team at Harmonic stayed committed and focused on building a device that could be a game-changing development in the way therapists work with patients who have suffered strokes. Testing with stroke patients is being planned at five top rehabilitation hospitals across the country, ushering in a new era in rehabilitation for stroke patients.