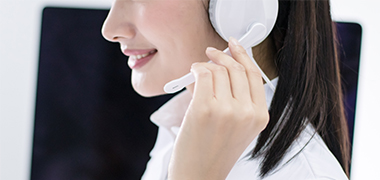
- Contact:Minister Xu
- Mobile:13841408476
- Tel:024-44837288
- Fax:024-44837004
- E-mail:xuming58@126.com
- Web:wanderlustamericana.com
- Address:No.110 XiangHuai Road
Benxi Economic Development Zone
Liaoning Province
Upgraded rotor bearings offer improved wind-turbine efficiency
02 Sep,2019
By Andreas Bierlein, Schaeffler Technologies GmbH & Co. KG
& Antonio Silverio, Schaeffler Group USA Inc.
In an effort to increase the reliability, durability and efficiency of wind turbines, Schaeffler has upgraded its entire lineup of spherical roller bearings (SRBs) for the turbine’s rotor shaft.
By using data compiled from 10,000 wind turbines, a thorough investigation was performed on several damage patterns and appropriate countermeasures and solutions were developed. These new SRB designs offer high wear resistance and considerably lower friction torque and operating temperatures — thereby significantly extending the turbine’s operating life.
Rotor shaft bearings are subjected to a range of dynamic loads, especially high axial loads.
Robust design
Because the rotor bearing is a critical component inside wind turbines. Schaeffler has substantially optimized its array of standard SRBs to further improve their performance.
The initial design improvements focused on two areas: The first step was to modify the profiles of both roller and raceways to achieve the lowest contact stresses even under the most extreme conditions. The second step was to design a central rib for the inner ring that increases axial stiffness and drastically reduces the roller’s excessive axial displacement, which is a main contributor to the premature wear observed on all rollers and raceways.
These new SRB designs have successfully completed a comprehensive range of tests as part of their validation for Schaeffler “X-life” seal of quality. of quality. The validation steps required for this have been certified by the German certification body for wind, Germanischer Lloyd (GL certificate GL-CER-002-2015). A patented asymmetrical spherical roller bearing (ASRB) design was also developed to further improve turbine efficiency.
The ASRB significantly increases the axial load carrying capacity while achieving a more balanced internal load distribution between both roller rows. The improved load distribution between the roller rows provides increased resistance against plastic deformation and significantly extends the bearing service life.
Featuring two different contact angles, the ASRB has a twofold load-carrying capacity. Axial loads are carried by the higher contact angle row side (downwind), while radial loads are supported mostly by the lower contact angle row side (upwind).
Operating data investigation
During the investigation of failed bearings, it was noted that a significant percentage of failures occurred mostly in locating bearings of the 3-point as well as 4-point support rotor shaft systems. Also, most of the damage was concentrated on the axially loaded row (downwind) of the locating bearings. The damage, which was found to be mostly at surface level, is classified in accordance with ISO15243 as either fatigue occurring near the surface (surface distress), or abrasive wear.
Schaeffler’s innovative asymmetric spherical roller bearing generates lower axial displacements, which substantially decreases the risk of damage to the bearing rollers and raceways.
Abrasive wear in wind-turbine main bearings operating under random conditions is already a widely recognized problem. This type of damage is primarily caused by varying shaft speed and loads that can lead to a very thin or nonexistent lubricating film. If the separating lubricant film between the roller and raceways surfaces is allowed to degrade, micropitting, smearing and, eventually, extensive damage at surface levels will be the result.
A comprehensive battery of in-house test simulations was performed to define the best solution to the damage patterns found near the surface. Several relevant bearing features were identified, simulated, and tested with state-of-the art tools and testing equipment. A variety of solutions were devised and implemented to reduce or even eliminate the surface wear caused by the borderline lubricating conditions.
One of the first counter-measures was to develop and validate a lubricant formulated with the proper load-carrying properties for a variety of operating conditions, including low shaft speeds and extreme loads. In addition to improving the lubrication conditions, a strong emphasis was placed on optimizing the bearing design with enhancements such as extremely strict surface finish limits and special roller coatings. Finally, all manufacturing steps and production processes were reevaluated and optimized.
The result: new SRB designs that offer far greater resistance to wear caused by poor lubricating conditions or even particle contaminants.
nstalling an asymmetric spherical roller bearing can reduce the axial forces on the gearbox’s planet carrier bearings by 70%.
Design improvements
As mentioned above, the design of the standard SRB was optimized by improving the quality of the surface finish.
Other design enhancements included:
Optimizing the osculation (i.e. the roller-to-race conformity) to obtain the lowest contact pressures
Using rollers with logarithmic profiling to reduce surface damage in the most critical contact areas
Optimizing the internal clearance to both reduce the rotor shaft displacement under heavy thrust loads and improve the load-per-roller distribution
Sdding an inner ring central rib to increase axial rigidity, improve contact pressure distribution throughout all rollers, and reduce surface damage.
In addition to optimizing its existing standard designs, Schaeffler developed and patented an entirely new bearing solution for mainshaft bearings in wind turbines: the asymmetric spherical roller bearing. With its different contact angles, this design innovation improves the load distribution between both bearing rows, lowers the contact pressure and friction torque, and increases axial stiffness by approximately 50%.
The increased axial stiffness results in a drastic reduction of the main shaft’s axial displacement, less axial sliding and skidding of the rollers, and increased reliability for the gearbox bearings and torque arm elastomers mounts. Further improvements can be realized by applying optional coatings such as Triondur C diamond-like carbon coating on the rollers for wear resistance as well as Durotect CK chromium coating applied to the inner ring to prevent fretting corrosion.
Validation
Schaeffler’s new ASRB design was subjected to an extensive battery of validation tests, both in-house as well as in the field. Compared with the standard design, the test results on the ASRB confirmed a 50% reduction in axial displacement, improved roller load distribution on both bearing rows, a 70% reduction in the forces transmitted to the gearbox planet carrier bearings, and a 67% increase in rating life.