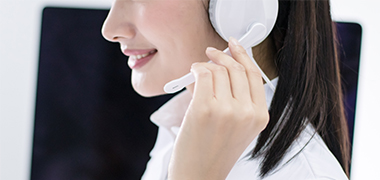
- Contact:Minister Xu
- Mobile:13841408476
- Tel:024-44837288
- Fax:024-44837004
- E-mail:xuming58@126.com
- Web:wanderlustamericana.com
- Address:No.110 XiangHuai Road
Benxi Economic Development Zone
Liaoning Province
Wind turbine reliability dashboard co-developed by SKF and Boralex will help reduce operating costs
30 Aug,2019
SKF and Boralex jointly announce the co-development of a new solution for wind turbine operators named “Wind Reliability Dashboard”. This combines data from multiple sources, including condition monitoring and manufacturing information for spare parts, allowing operators to optimise the efficiency of each wind farm, as well as improving reliability and predictability of defaults.
SKF is developing, in partnership with Boralex - a leader in the Canadian market and France’s largest independent producer of onshore wind power - a new dashboard to help wind farm operators optimize the proficiency of wind turbines. The dashboard will also improve operators ability to reduce costs and make long term planning decisions based on in-depth data drawn from a range of critical sources; these include condition monitoring systems, estimated remaining useful life and the lead-time of replacement parts.
The Wind Reliability Dashboard is an evolution of SKF’s current condition monitoring and predictive maintenance tools. It extends existing capabilities by allowing data to be captured and analysed from all forms of rotating systems in each turbine, from both SKF and other CMS providers (Condition Monitoring System).
The Wind Reliability Dashboard is currently being tested in the field by Boralex, SKF’s development partner. Jer?me Gardyn, CMS Analyst at Boralex, says: “We have been working closely with the SKF engineers on every step of the project from the definition of functional needs, through the core development of the device, to real-life condition tests, in order to help SKF refine the dashboard model.”
Typically it keeps track of components actual and remaining service life, based on previous detection CMS cases. This allows the creation of a reliable component library which allows the move to predictive maintenance via better risk management.
The dashboard also captures information from maintenance systems as well as from the supply chain; for example, it allows the matching of replacement spare parts lead-time with remaining useful life of the component.
Ultimately, it can provide external Systems like CMMS (Computerized Maintenance Management Systems) the key indicators for maintenance best practices, components MTBF (Mean Time Between Failure) & lead time.
Jonathan Day, Analytics and Digitalization Development for SKF, explains: “Wind farm operators are under increasing pressure as growing numbers of turbines fall out of warranty and as market price for renewables gets more and more challenging. Identifying ways to reduce OPEX and protect margins is therefore crucial. This is the driving factor behind our Wind Reliability Dashboard, which will help each operator improve the efficiency of their business. The dashboard allows operational and business management teams to communicate far more effectively about critical turbine maintenance and planning issues. It also makes it easier to identify and predict drive train issues, manage spare parts logistics and reduce risk, by enabling data driven decision-making.”
Jan Levander, Project Manager Supply Chain 4.0, adds “we have in the dashboard also managed to add direct links into SKF supply chain availability information using Supply Chain 4.0 logic to ensure and optimize stock planning and to reduce overall cost.”
Giannino Martin, Operational Excellence Deputy Director for Boralex concludes: “We see the Dashboard as an effective and innovative method of streamlining critical elements in our business. Working with SKF is giving us access to new in-depth data, which we believe will be instrumental in helping us reduce our operating costs while increase reliability and predictability of the production, so providing even a better service to all our customers.”