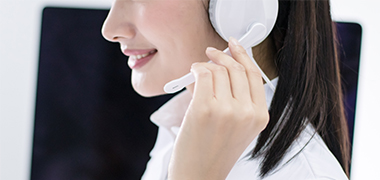
- Contact:Minister Xu
- Mobile:13841408476
- Tel:024-44837288
- Fax:024-44837004
- E-mail:xuming58@126.com
- Web:wanderlustamericana.com
- Address:No.110 XiangHuai Road
Benxi Economic Development Zone
Liaoning Province
Predictive maintenance for LV motors
22 Aug,2019
In last month’s column, Rob Wood, ABB’s UK sales manager for LV motors and generators, looked at three types of maintenance strategy. This month, he examines what predictive maintenance means in practice for maintaining LV motors.
A predictive maintenance strategy uses the actual condition of equipment to plan what maintenance needs to be performed and when it should be carried out. Various machine components are monitored by various on- and off-line measurements. Because these measurements are used to assess the condition of the motor, the process is known as "condition monitoring".
The most common parameters measured are:
? power, voltage, currents and frequency;
? vibrations; and
? temperature
Readings can be taken on-line, or while the machine is running and off-line, during a scheduled maintenance break.
Deciding what needs to be measured and whether the readings are taken on- or off-line depends on the size and power of the motor being monitored. It is here that the differences between low- and high-powered motors become more apparent.
With lower-power motors, failures tend to be due to issues with the bearings, whereas with high-power motors, the problems tend to lie more in the stator windings and rotor bars – the parts of the motor under the highest electrical and mechanical stresses.
The condition of these internal active parts usually requires direct inspection and measurement, which is typically performed off-line, in addition to the on-line measurements taken while the machine is running.
In contrast, the windings in low-power, low-voltage motors are under less electromechanical stress and rarely need internal inspection. This means that the condition can usually be assessed adequately using on-line monitoring only.
Condition monitoring has been greatly simplified by the advent of smart sensors. These pocket-sized devices can be retrofitted easily to any LV motor, without needing any extra wiring. They monitor key parameters such as motor temperatures and vibrations and transfer the data in real time to a secure server in the cloud. The server analyses the data to produce diagnostic information and performance alerts that can be sent directly to the user’s smart device. A simple traffic light display gives a quick overview of the motor’s condition, allowing necessary maintenance to be planned and executed before the motor’s condition worsens and causes an unplanned production stop.
Knowing this information allows maintenance resources to be deployed more efficiently which, in turn, improves performance and extends the lifetime of the motor.