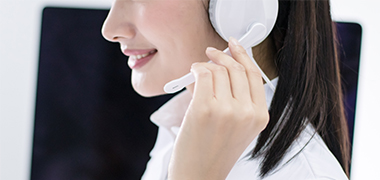
- Contact:Minister Xu
- Mobile:13841408476
- Tel:024-44837288
- Fax:024-44837004
- E-mail:xuming58@126.com
- Web:wanderlustamericana.com
- Address:No.110 XiangHuai Road
Benxi Economic Development Zone
Liaoning Province
Project-managed approach to shaftline repair minimises lost time and income
16 Aug,2019
Damage to shaftlines and associated equipment can be costly in both time and money, so being able to resolve problems in this area swiftly when they occur is of vital importance to vessel owners and operators.
As owners of arguably one of the largest portfolios of seal and bearing products and solutions on the market, W?rtsil? Seals & Bearings is seeking to remedy this with its recently launched Shaft Line Repair Services. Operations Manager, W?rtsil? Seals & Bearings Shaft Line Repair Services, Simon Wiles explained why such a service is necessary and how it can benefit shipowners and operators.
Mr Wiles sees two main scenarios where the repair service is needed:
“One is when an owner or a ship operator reports a common symptom,” he says, explaining: “Common symptoms can be anything from a leaking seal to a worn or overheating bearing, or just noise and vibration.”
Such problems may appear minor but they can be persistent, and if not investigated can lead to serious outcomes, says Mr Wiles, adding: “It could lead to a major breakdown of a component on the shaftline, which could take the ship out of service for a considerable amount of time.”
“The other scenario is if an operator has a major incident, which could be anything from fire, to flooding or grounding, or just a major breakdown of a component.”
An example of the system being applied was a project from earlier in 2019 for a customer in Scandinavia, says Mr Wiles. This customer had noted recurrent leaking seals and came to W?rtsil? Seals & Bearings for assistance when simply replacing the seals failed to resolve the problem.
A team of alignment engineers was sent on board the vessel to perform a number of measurements, including jack-up tests using automated load cells. Based on these investigations, W?rtsil? Seals & Bearings recommended the vessel be sent to dry dock for further investigations. These showed that the aft bearing had signs of wear and the shafts on the vessel were out of tolerance. While the vessel was in dry dock, the customer took the opportunity to upgrade the couplings to W?rtsila’s high friction couplings, straightened the bent shafts and reconditioned the aft and forward seals, all of which was managed through W?rtsil?’s end-to-end service.
In a typical case, W?rtsil? will send alignment specialists on board to carry out investigations to determine what work is needed, based on which project managers will ensure all relevant parts from various factories are coordinated and delivered together with the field services required for installation.
“When I say end-to-end what I mean by that is we carry out investigations, we do the root-cause analysis, and then we prepare the reports and provide customers with the work scopes that are required to correct whatever issue there is,” says Mr Wiles, adding: “And then we project-manage that repair work.”
Minimising downtime is a key argument in favour of W?rtsil?’s holistic approach to shaft-line maintenance, which benefits from the company’s manufacturing expertise and use of automated processes and robotics, so that bearings, dependent on size, can be repaired within as little as a day. Delays are also kept to a minimum thanks to the company’s wide product portfolio, wide repair service expertise and globally available service engineers, all of which are co-ordinated by project managers.
“What we’re doing with our project managers is giving the customer a centralised point of contact for all of our resources, and we can then be highly efficient in the delivery of services and parts so they arrive just in time to ensure that the vessel gets out of drydock as soon as possible,” says Mr Wiles.