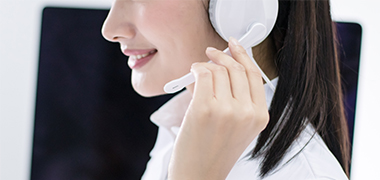
- Contact:Minister Xu
- Mobile:13841408476
- Tel:024-44837288
- Fax:024-44837004
- E-mail:xuming58@126.com
- Web:wanderlustamericana.com
- Address:No.110 XiangHuai Road
Benxi Economic Development Zone
Liaoning Province
In every revolution, it’s the details that matter from SKF
03 Jul,2019
Powertrain engineers are pursuing innovative solutions to age old problems of efficiency, cost and reliability, SKF’s Carole Girardin, Global Product Devolopment and Engineering Manager, explains.
The automotive powertrain is in a state of flux. While engineering teams rush to develop new EV and hybrid architectures, they must continue to squeeze every ounce of efficiency from IC engines and transmission designs. This multilane development strategy has many miles to run.
Although governments around the world are announcing plans to phase out petrol and diesel engines over the coming decades, combustion engines, combined with different levels of hybridization, are still expected to account for more than 90 percent of the global passenger car market until at least the middle of the next decade.
SKF has been involved in the design of bearings and other components for automotive applications since the first automotive revolution. Today, the company continues to invest heavily in technology, product development as well as application support in the sector, helping OEMs and their suppliers solve today’s most pressing engineering challenges.
Traditional IC powertrains remain a significant focus of SKF’s work in the automotive sector. The company is developing and testing new solutions that reduce friction in order to improve engine efficiency, fuel consumption and emissions. In particular, recent work has focussed on novel solutions addressing customer needs in camshaft and balancing shaft applications.
Working with a major European OEM, for example, SKF helped to create a new bearing package that significantly reduces losses from friction in a balancing shaft application.
The new solution allowed the manufacturer to replace its traditional journal bearings with SKF rolling bearings. That change has reduced powertrain friction and cut CO2 emissions by more than 1 percent. SKF also helps manufacturers to optimize component packaging and assembly processes. In this application, carbonitrided heat treatment was used to increase the subsurface fatigue resistance of the bearings, allowing a longer operating life without any increase in bearing size.
Another OEM was looking for ways to improve efficiency of its camshaft architecture without impacting too much the packaging. Working with SKF, the OEM replaced its existing plain bearing solution with a thin section ball bearing. Once again, a carbonitrided surface treatment on the bearings was used to improve surface fatigue characteristics in the demanding operating environment, which required the bearings to run in oil-polluted soot from the engine. The new solution allowed the OEM to significantly reduce the friction losses generated by axial load on the shaft. This change helped them to meet the latest European standards for CO2 and emissions.
An important part of SKF’s development work in applications like these is its use of advanced proprietary simulation software to optimise bearing component design. The company continues to develop computational approaches for the estimation of bearing lifetime and advanced dynamic simulation to predict bearing components’ behaviour inside powertrain systems. During the development process, solutions can also be validated using physical tests to determine bearing lifetime under varying lubrication and contamination conditions, friction as well as noise and vibration characteristics.
The coming years may be the most dynamic and challenging period in decades for automotive powertrain engineering. With industry-leading expertise in materials science, analysis, design and component testing, SKF is working with companies across the sector to solve problems, develop innovative solutions and push the limits of performance, efficiency and reliability.